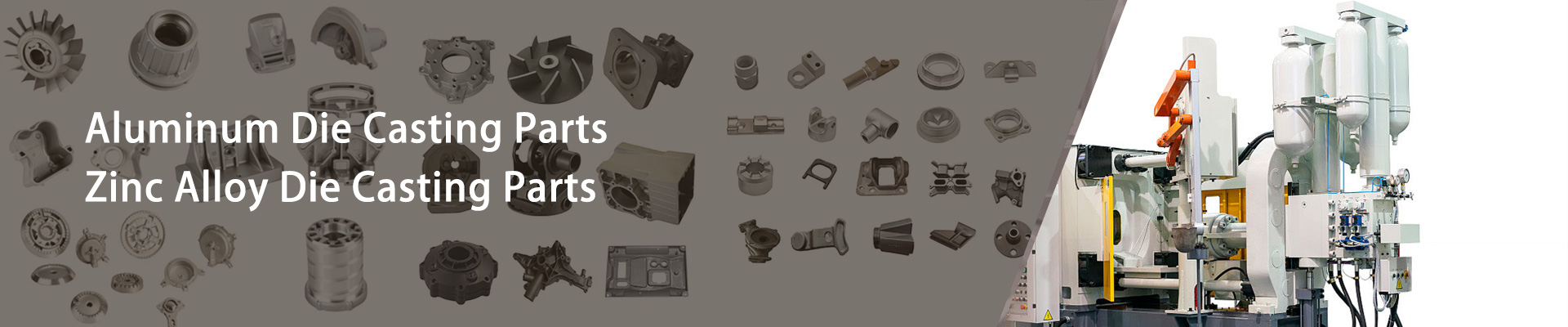
डाई कास्टिंग प्रक्रिया का परिचय और अनुप्रयोग (भाग 1)
2023-12-26 04:24
प्रक्रिया विशेषताएँ:
(1) धातु या मिश्र धातु तरल को उच्च दबाव में सांचे में भरा जाता है और एक निश्चित दबाव में क्रिस्टलीकृत और ठोस बनाया जाता है, आमतौर पर कई मेगापास्कल से लेकर कई दसियों मेगापास्कल तक, 200 एमपीए तक। यह उच्च गुणवत्ता, उत्कृष्ट यांत्रिक गुण और कास्टिंग की अच्छी वायुरोधीता सुनिश्चित करता है।
(2) धातु या मिश्र धातु तरल तेज गति से मोल्ड को भरता है, इंजेक्शन की गति आमतौर पर 10-30 मीटर/सेकेंड के बीच होती है, जो 80 मीटर/सेकेंड तक पहुंच जाती है। इसके परिणामस्वरूप बहुत कम कास्टिंग और मोल्डिंग समय (0.001-0.2s) होता है, जिससे उच्च उत्पादकता होती है।
(3) मोल्ड में बड़ी ताप क्षमता और तीव्र ताप चालन होता है, जिसके परिणामस्वरूप घनी ढलाई संरचनाएं, बारीक क्रिस्टलीकरण, उत्कृष्ट यांत्रिक गुण और अच्छा घिसाव और संक्षारण प्रतिरोध होता है।
(4) उपरोक्त विशेषताओं के कारण, धातु या मिश्र धातु के तरल पदार्थों को अपेक्षाकृत कम तापमान पर, अर्ध-तरल तरल पदार्थों के साथ भी, पतली दीवारों और जटिल आकृतियों के साथ कास्टिंग का उत्पादन किया जा सकता है।
लाभ:
(1) डाई-कास्टिंग की उच्च आयामी और आकार परिशुद्धता। अलौह मिश्र धातु डाई-कास्टिंग की सटीकता आम तौर पर जीबी 1800-70 के अनुसार आईटी11~आईटी14 स्तर तक पहुंच सकती है, कुछ आईटी9 स्तर तक पहुंचते हैं, जिससे उत्कृष्ट विनिमेयता सुनिश्चित होती है।
(2) डाई-कास्टिंग की चिकनी सतह, जीबी/टी 1031-83 के अनुसार सतह खुरदरापन रा0.80~0.4um तक पहुंचती है, और अधिकतम रा0.21m।
(3) डाई-कास्टिंग पतली दीवार वाली (0.3 मिमी जितनी पतली), गहरी-गुहा, छोटे छेद वाली जटिल संरचनाएं (न्यूनतम व्यास 0.7 मिमी), धागे (न्यूनतम पिच 0.75 मिमी), पैटर्न, टेक्स्ट और उत्पन्न कर सकती है। विभिन्न सामग्रियों के साथ कास्टिंग।
(4) डाई-कास्टिंग विभिन्न आकृतियों, आकारों और सामग्रियों के एम्बेडेड भागों के साथ कास्टिंग का उत्पादन कर सकती है, कीमती धातुओं को बचा सकती है, प्रसंस्करण समय को कम कर सकती है, विविध आवश्यकताओं को पूरा कर सकती है, उत्पाद अनुप्रयोगों का विस्तार कर सकती है और विनिर्माण प्रक्रियाओं को सरल बना सकती है।
(5) कम भरने के समय और उच्च दबाव में तेजी से ठंडा होने और जमने के कारण, डाई-कास्टिंग में घनी संरचनाएं, महीन सतह परतें, उच्च तन्यता ताकत (रेत कास्टिंग से 25% ~ 30% अधिक), अच्छी कठोरता, पहनने का प्रतिरोध होता है। और संक्षारण प्रतिरोध।
(6) उच्च सामग्री उपयोग। उच्च आयामी सटीकता और कम रा मूल्यों के साथ डाई-कास्टिंग को आमतौर पर मोल्डिंग के बाद बहुत कम या कोई अतिरिक्त प्रसंस्करण की आवश्यकता नहीं होती है, जिसके परिणामस्वरूप उच्च सामग्री उपयोग (80-95% तक) और सरलीकृत विनिर्माण प्रक्रियाएं होती हैं।
(7) उच्च उत्पादकता। आधुनिक डाई-कास्टिंग ऑपरेशन अत्यधिक यंत्रीकृत और स्वचालित हैं, जिससे उत्पादन चक्र कम और उच्च दक्षता होती है, जो इसे बड़े पैमाने पर उत्पादन के लिए उपयुक्त बनाती है।
(8) दीर्घ जीवन मरो। उन्नत डाई सामग्री और कुशल सुदृढ़ीकरण विधियां डाई जीवन को महत्वपूर्ण रूप से बढ़ाती हैं, जिसमें जीवनकाल सैकड़ों हजारों से दस लाख से अधिक कास्टिंग तक पहुंच जाता है।
नुकसान:
(1) पारंपरिक डाई-कास्टिंग प्रक्रियाओं का उपयोग करते समय डाई-कास्टिंग में बुलबुले या सरंध्रता हो सकती है। यदि मजबूती के लिए ताप उपचार लागू किया जाता है तो धातु तरल में परिष्कृत न की गई अशुद्धियाँ और गैसें समस्याएँ पैदा कर सकती हैं। जिन डाई-कास्टिंग के लिए ताप उपचार की आवश्यकता होती है, उनके लिए वैक्यूम मेल्टिंग और वैक्यूम डाई-कास्टिंग की आवश्यकता होती है।
(2) डाई-कास्टिंग मशीन और मोल्ड निर्माण स्थितियों द्वारा वजन और आकार की सीमाएं लगाई जाती हैं, जिससे आंतरिक संरचनाओं के साथ जटिल आकार की कास्टिंग के लिए चुनौतियां पैदा होती हैं।
(3) डाई-कास्टिंग के लिए उपयुक्त सीमित मिश्र धातु प्रकार। डाई-कास्टिंग मोल्डों का खराब उच्च तापमान प्रदर्शन और काम करने वाले तापमान पर प्रतिबंध उच्च पिघलने बिंदु वाली धातुओं, जैसे कच्चा लोहा, कार्बन स्टील, मिश्र धातु इस्पात, स्टेनलेस स्टील, आदि के उपयोग को सीमित करते हैं।
(4) छोटे बैच के उत्पादन के लिए उपयुक्त नहीं है। डाई-कास्टिंग मशीनों और सहायक उपकरणों की उच्च लागत, डाई के लिए लंबे डिजाइन और विनिर्माण चक्र, और उच्च एकल-टुकड़ा उत्पादन लागत इसे छोटे-बैच उत्पादन के लिए अलाभकारी बनाती है।
नवीनतम मूल्य प्राप्त करें? हम जितनी जल्दी हो सके जवाब देंगे (12 घंटे के भीतर)